Calibrating a route is important to ensure that your m-measures are reliable and can be used to accurately locate events.
Calibration
It is possible to adjust route measures to correspond with known measure locations using a procedure called calibration. Calibration adjusts route measures by reading measure information stored as an attribute in a point feature class. Each point falls on the particular route it calibrates or within a given tolerance of the route line. Many points can be used to calibrate a single route.
During the calibration process, a new vertex is created where each calibration point intersects the route. The measure value on these new vertices corresponds to the measure value stored as a point attribute. The measure values on other preexisting route vertices can be interpolated and/or extrapolated.
The calibration process creates a new vertex for every point within the specified tolerance, as shown below. The measure at each new vertex will correspond to the point's measure value. You control whether the remaining vertices will have their measures interpolated or extrapolated.
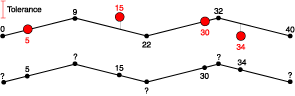
Either whole or partial routes can be calibrated. You can choose to interpolate between the input points, extrapolate before the input points, extrapolate after the input points, or use any combination of these three methods.
Calibration ratio
For the measure value on a vertex to be interpolated or extrapolated, a calibration ratio is needed. There are two ways this ratio can be determined. The first method uses the shortest-path distance between the input points.
The second method uses the existing measure distance between the input points. This method is useful when the length-to-measure ratio on the input route is not consistent and you are using the calibration process to fine-tune a route's measures.
When calibrating disjointed routes, you can choose to ignore the distance of the spatial gap between the parts. If you choose to ignore spatial gaps, route measures will be continuous. If you want the spatial gap incorporated in the measures, the gap distance is the straight-line distance between the endpoints of the parts. The units of the gap will be that of the output coordinate system, which may or may not be the same as the measure units. Ignoring spatial gaps is only a valid choice when using the shortest-path distance method of calibration.